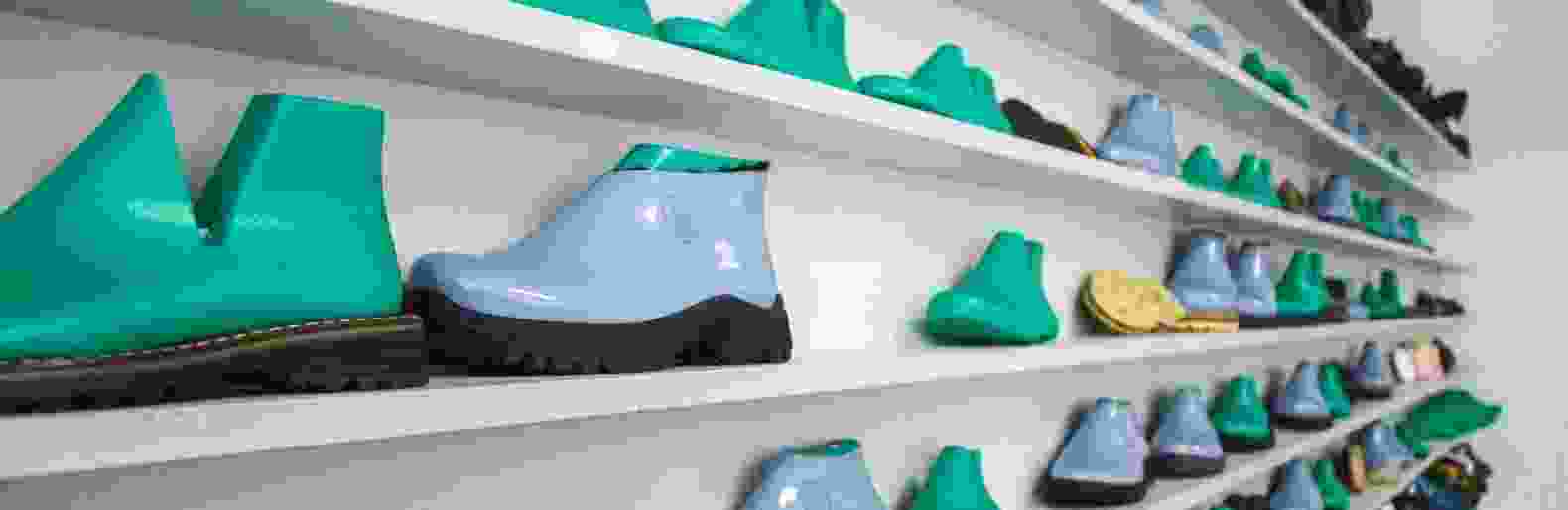
В специальном проекте 061 продолжает рассказывать, как на запорожских предприятиях создают ту или иную продукцию. Ранее наши корреспонденты показывали производства кваса, пива и шифера, стали, а также нынешнее состояние ЗаЛКа. В этот раз 061 побывал на запорожской фабрике «Мида», на которой более 2000 специалистов изготавливают обувь для всей Украины, а также на экспорт.
Запорожская обувная фабрика – предприятие полного цикла. Здесь производство начинается от придумывания идеи модельерами до реализации в торговую сеть, насчитывающую более 100 магазинов.
На фабрике производством обуви занимаются 1800 сотрудников. Еще 500 людей работает в филиале обувной фабрики в Васильевке.
Колодка
Обувь начинается с колодки – приспособления, которое в процессе производства придает обуви необходимую форму. Мастер с учетом физических параметров стопы будущего клиента, а также знаний ортопедии обтачивает полиэтиленовую заготовку до нужных размеров. Ошибка даже в миллиметре – это уже много, – говорят на фабрике.
После изготовления пробной колодки, если говорить языком обывателя, кожаный чулок, который повторяет форму колодки, испытает тестовая группа людей с разной полнотой ноги. В дальнейшем колодку будут дотачивать до нужных размеров, пока колодка не будет соответствовать всем параметрам.
На каждой колодке указано буквенное или цифровое название фасона, а также – размер.
Цех колодок
В последующем колодка станет центральным компонентом работы. В производстве для каждой пары обуви нужна своя пара колодок. Созданную типовую модель в отдельном цеху тиражируют на специальном оборудовании. На станках сначала вытачивается черновая модель.
Внутрь вставляют металлические «замки» – они необходимы, чтобы в дальнейшем вынуть ее из готовой обуви.
Напоследок работники цеха вручную дотачивают колодку, сверяя размеры с помощью контрольных шаблонов.
Подошва
На очередном этапе производства группа модельеров разрабатывает подошвы. Они вручную прорисовывают все: от высоты подъема до особенностей рисунка. Дизайн подошвы обусловлен последними тенденциями моды, технологическими особенностями материалов, требованиями к ортопедии и безопасности, запросами клиентов. Сейчас здесь создают подошвы, которые будут носить в 2019-м году.
Нарисованное изображение подошвы превращают в чертеж, трехмерную модель, а затем – в литейную форму. Процесс создания подошвы от начала до готовой продукции может занимать 6 месяцев.
Цех литья подошв
Готовые пресс-формы устанавливают в литьевые машины. Внутри разогревается сырье – пластиковые гранулы – и заливается в форму. Через несколько минут литейщик достает одну пару подошв.
На каждой подошве – маркировка: указатель бригады или личное клеймо рабочего. Таким образом осуществляется контроль всех этапов производства.
Подошвы бывают одно-, двух и трехцветные.
Цех по производству стелек
В отдельном цеху занимаются изготовлением основных стелек для обуви. В дальнейшем на них будет осуществляться монтаж заготовки: ее закрепят между колодкой и кожаной частью обуви.
Стельки здесь вырезают из специального обувного картона. Внутри него – эластичные полимеры, благодаря чему он сохраняет свою форму. Между слоями стельки крепят супинатор – это добавляет стельке жесткости и придает форму.
В этом цеху могут производить до 5 тысяч стелек в день.
Модельеры моделей обуви
Одна пара может содержать до 50 и более различных деталей. Все эти особенности на обувной фабрике придумывают мастера-модельеры.
Как выглядит создание модели? Один из вариантов – колодку обклеивают бумажным скотчем, а затем по нему рисуют образ будущего изделия. Когда рисунок завершен, скотч срезают и получают бумажный эскиз модели. Второй вариант – сразу строить 3D модель по колодке, используя специальные программы.
На столе – бумажный эскиз обуви в разрезе. Одна пара, в одном размере.
Раскройный цех
Раскройщикам готовят металлические резаки – они повторяют форму и размер будущих элементов изделия. На каждый размер и модель – свой набор резаков.
Мастера с помощью пресса вырезают из большого куска кожи необходимые детали будущей пары, экономно и рационально используя материал. Это элементы будущей конструкции обуви.
Цех пошивки
Сбор верха обуви проходит в пошивочном цехе. Швеи сшивают кожу, подкладку, мех, крепят фурнитуру и молнии, собирая разрозненные детали в заготовку.
Затем на специальном агрегате происходит формовка: под действием высокой температуры и пара кожаной заготовке придают определенную форму.
На колодку закрепляют стельку. Затем по отдельности происходит затяжка носочной, задней и боковых частей обуви. В результате на колодке получаем модель сформованной обуви без подошвы.
Работник сначала обезжиривает, а потом наносит на поверхность подошвы клей.
Перед приклеиванием на обуви прорисовывают контур подошвы. Нижнюю часть обуви фигурно шлифуют, чтобы хорошо приклеилось.
На этом этапе заготовку приклеивают к подошве. Это происходит под действием давления и определенной температуры.
Некоторое время обувь выстаивается на колодке. К слову, модели дорогой итальянской обуви могут выстаиваться на колодке несколько месяцев.
Мастер вынимает колодки из обуви.
Работник фабрики на специальном агрегате «вытягивает» голенище женских сапог.
На финальном этапе занимаются вклейкой внутренних стелек, шнуровкой, тщательной проверкой качества и упаковкой.
Текст — Андрей Вавилов, фото — Слава Чиженок
Читайте также:
- Как на запорожском заводе готовят квас: экскурсия на производство, — ФОТОРЕПОРТАЖ
- Как на запорожском заводе готовят пиво: экскурсия на производство, — ФОТОРЕПОРТАЖ
- Как на запорожском заводе делают шифер: экскурсия на производство, — ФОТОРЕПОРТАЖ
- Как на «Запорожстали» железную руду превращают в сталь: экскурсия на производство, — ФОТОРЕПОРТАЖ
- Уникальный завод, который хотели уничтожить россияне:экскурсияна «ЗАлК», — ФОТОРЕПОРТАЖ